Urethane Casting Services
- Instant quoting available
- Durable parts with production-level quality
- Low-volume manufacturing in a wide range of materials
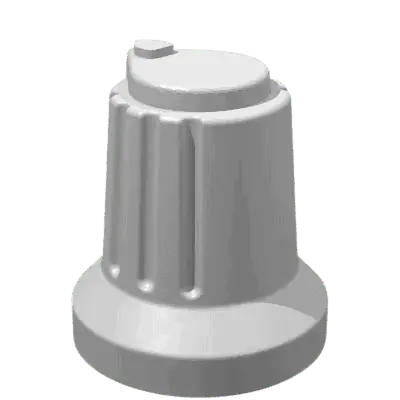
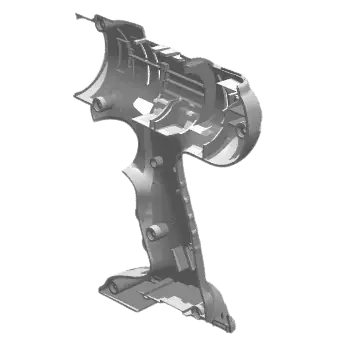
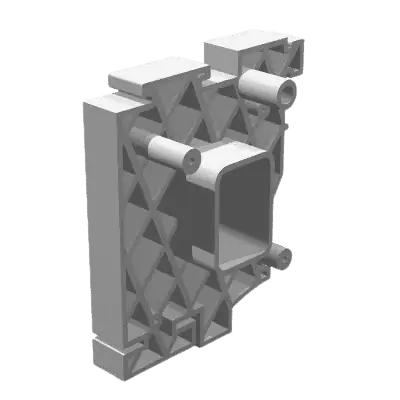
Start A New Casting Quote
STEP | STP | SLDPRT | STL | IPT | 3DXML | CATPART | PTC | PRT | SAT | PDF
Urethane Casting Services
Urethane casting is a manufacturing technology for producing rigid, flexible or rubber parts with final product quality. The process uses a reference (master) model and silicone molds to produce low-volume mass production parts at high speed and quality. Part dimensions depend on the accuracy of the master model, part geometry and molding material.
Silicone molding is an excellent alternative for insert molding in low volumes and offers a wide variety of materials. It is also used as a bridge production technology between 3D printing and injection molding to effectively balance quality, cost and time.
Urethane casting parts can be produced transparent or in various colors, and surface quality and strength can be improved by post-processing.
Urethane Casting Applications
Low volume production
It is an ideal production method for low-volume production or pre-series production of final products without the need for plastic injection molds with high upfront costs.
Advanced rapid prototyping
Cost-effective molds make it easy and affordable to make the necessary changes to the design. It also allows you to test designs with a variety of materials, using the same mold.
Market testing
Silicone molding technology is one of the most suitable options for functional testing, strength testing and design verification, where you can achieve perfect surfaces for end-use product functionality. Enter the market confidently with flexible material options, relatively few manufacturability constraints and accurate revisions implemented with fast feedback.
Materials
- ABS-like
- ABS (PR2000)
- ABS (PR700)
- ABS (PR794)
- HDPE, PP-like (PR777)
- PR777 + 15% Synfill, HDPE, PP
- PR777 + 20% Synfill, HDPE, PP
- PR777 + 25% Synfill, HDPE, PP
- PC,ABS (PRS100)
- PMMA/PC-like
- Crystal HRI 35, PMMA/PC
- PRC1819, PMMA/PC
Advantages of Silicone Molding with Xometry
Lead times
Depending on the complexity of the part design and the required surface quality of your prototype, silicone molding can take 15-25 days.
Manufacturing volume
Vacuum casting is best suited to low-volume prototyping of up to 20 units made from a single mold. For more units, additional molds will be required and your project costs will go up.
Variety of materials
Start production with rigid, flexible, transparent or colored engineering plastics.
Skilled engineering team
Our experienced team of molding engineers will guide you through every step of the process.
Vacuum Casting Tolerances
Tolerance values in vacuum casting depend on part dimensions and design complexity. The table below provides example tolerances based on various dimension ranges*:
Dimensions (mm) | 0 — 25 | 25 — 50 | 50 — 75 | 75 — 100 | 100 — 125 | 125 — 150 |
Tolerance (mm) | ±0.3 | ±0.35 | ±0.4 | ±0.45 | ±0.5 | ±0.55 |
*The values provided are illustrative. Tolerances should be determined individually for each vacuum casting project based on 2D drawings and CAD models of the specific part. For parts larger than 150 mm, please supply a 2D drawing and discuss tolerance requirements with your account manager.
Description | Tolerance Notes |
Distance Dimensions | Irregular or overly-thick geometries may cause deviances or deflection due to shrinkage |
Surface Quality | Surface finish is externally smoothed to a satin or matte surface. Grow lines may be present on internal or difficult-to-access features. Polishing or custom finishes must be clearly defined and agreed upon at the point of order |
Feature Definition | Sharp corners and text may appear slightly rounded |
Size Recommendation | We can offer vacuum cast parts as large as 2,000 mm long |
Xometry: Source Your Casting Parts Online
All uploads are secure and confidential.